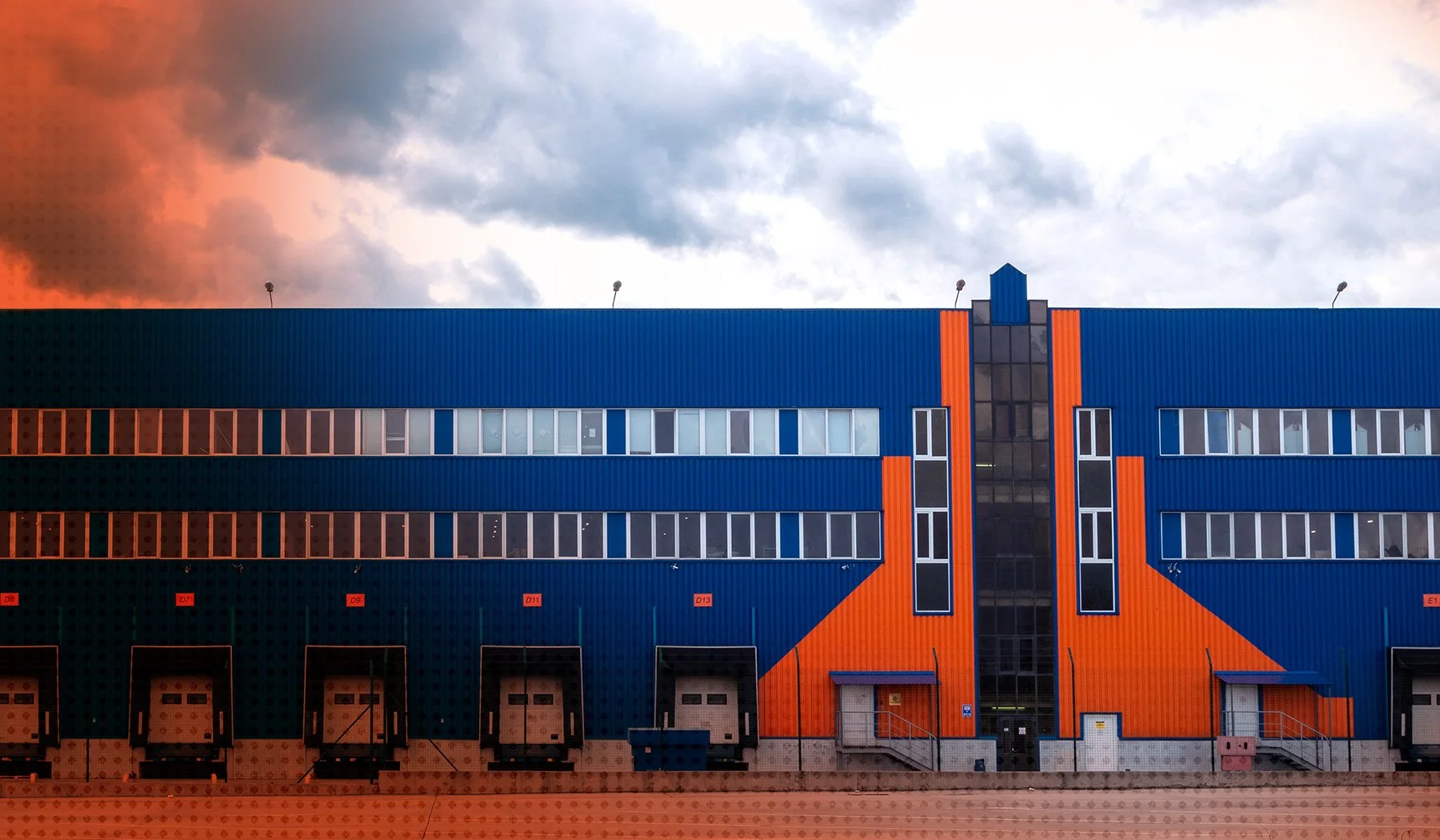
Warehouse & Inventory Management
Marblehead Consulting assists clients with defining warehousing and inventory needs, including services like pick & pack, kitting, and reverse logistics. We provide insights on industry best practices, distribution scenarios, vendor-managed inventory, and outsourcing benefits compared to in-house operations. We also cover efficient container management and handling reusable packaging returns, common in manufacturing.
Common Errors in Setting Up a WMS
-
• Receiving area too small – inadequate "holding space"
• Overlapping shipping and receiving areas
• Confusion between incoming and outgoing products
• No visibility to what's coming / being delivered or dropped off
• Poor labelling, inadequate paperwork
• Overcrowded computer terminals, stations, scales, etc.
• Inefficient picking paths (items purchased together are in distant locations)
• High-demand products easier to access and to load, lower demand products towards the back
• Pick instructions not in efficient sequence – not linear
• Warehouse inefficiencies lead to too much stock – built in buffers, too much overhead
-
• Leads to shortages during demand surges, seasonal spikes,
• Invest in predictive technologies – how much product at a given location!
• New technology only works with accurate data ( historical or real-time)
• New technology offers real-time updates helping to avoid back orders, which could trigger express shipping
• Add-on carrier rate and transit time comparisons – ensure Leads to shortages during demand surges, seasonal spikes,
• Invest in predictive technologies – how much product at a given location!
• New technology only works with accurate data ( historical or real-time)
• New technology offers real-time updates helping to avoid back orders, which could trigger express shipping
• Add-on carrier rate and transit time comparisons – ensure
-
• Shipping and storing proper products at the correct DC, in the proper quantities
• Choose best DC for types and distance of products being shipped (based on customer demand/density, etc)
• Inventory redistribution based on real-time data
-
• Solution needs to satisfy needs today and in the future – ability to scale
• Integration with ERP and TMS
• Offers transparency, visibility, and traceability (receipts, batch numbers, etc)
• Use location tracking methods – not lost, misplaced, or forgotten
• Allows you to share data with external partners
-
-
Automation for Improved Customer Service
-
Leads to more flexibility and faster picking and shipping times and your ability to scale.
-
Higher quality assurance (QA) consistency leads to improved customer service/satisfaction, a notable competitive advantage.
-
Regularly updated information as changes or delays are communicated early and more often, reducing overall warehousing costs.
-
Reduces or eliminates the need for backorders and rush shipments.
-
• Inventory age monitoring
• Inventory turnover rate
• Available-to-Promise (ATP) management
• Trace product movements and audit
• Integration with TMS – order management
• Integrated Labor Management systems (LMS)
• Integrated automated Storage and Retrieval Systems with
• Pick Assist
-
Robotics In Action
• Goods-to-Person (GTP)
• Automated Storage and Retrieval Systems (AS/RS)
• Automated Guide Vehicles (AGVs)
• Autonomous Mobile Robots (AMRs)
• Pick-to-Light and Put-to-Light Systems
• Voice Picking and Tasking
• Automated Sortation Systems